Finding the Perfect Flower: The Journey of Roses
It's not Valentine's Day without roses. See their journey from the farm to your loved one's heart.
Feb 03, 2023
From the Americas and Europe to Africa and Asia, millions of roses are cultivated every year for Valentine’s Day, Mother’s Day, and every occasion big and small. It’s a painstaking process as each plant must mature for as many as five years before it’s ready to produce a bloom that’s sellable in a store or usable by a florist.
But not all roses are created equal. Even those on a fully mature plant may not be suitable for a bouquet. Some may bloom too early or blossom into a disappointingly small flower. Other roses may look perfect, only to wilt in a vase after just a day.
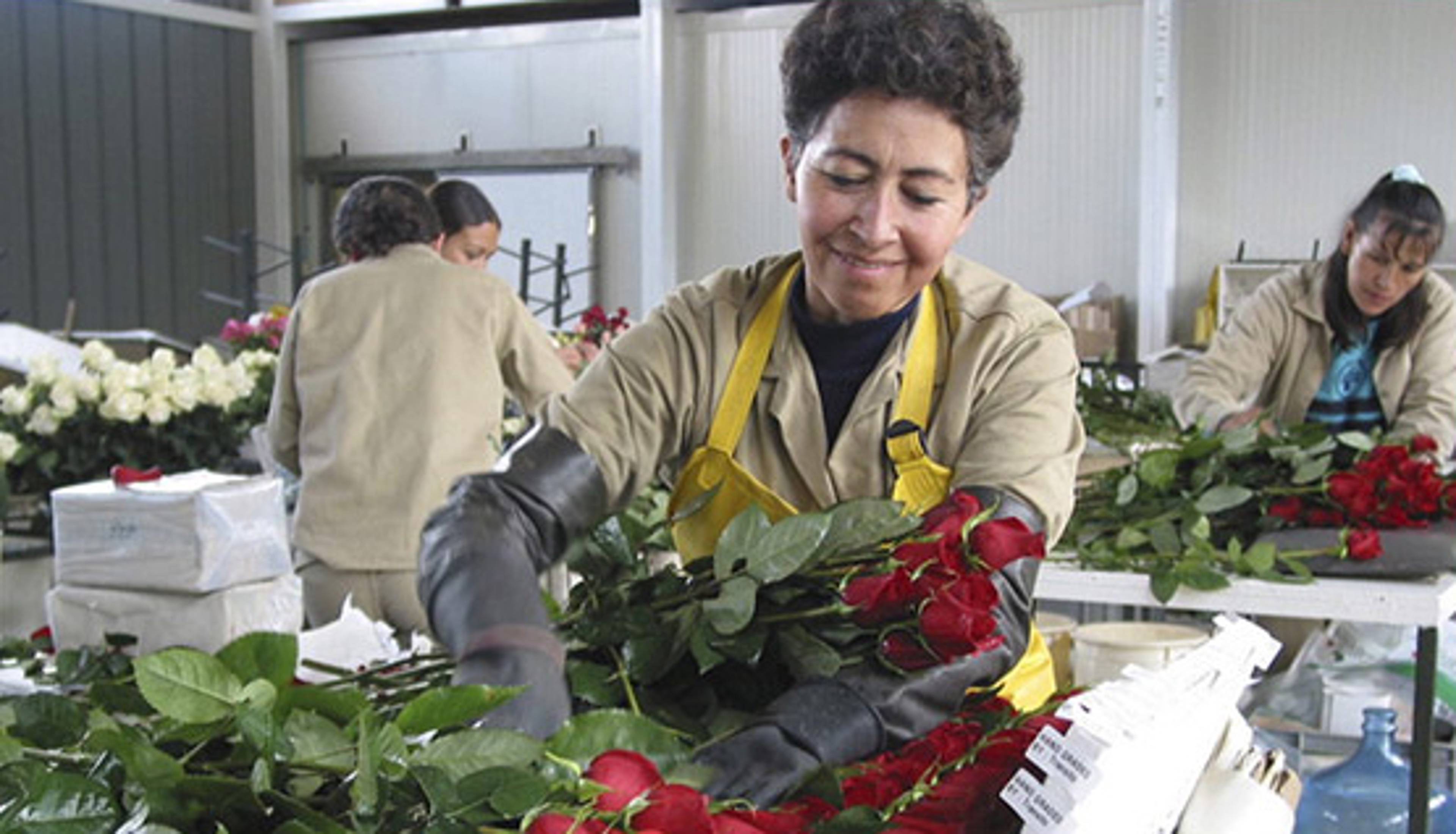
How do you pick a perfect rose? “No. 1, you start off with the right specs, the right freshness, and the right varieties,” says Kevin Cochran, vice president of procurement at 1-800-Flowers.com.
Cochran’s team is responsible for buying and ensuring the quality of millions of flowers each year. In the weeks leading up to Valentine’s Day in 2023, 1-800-Flowers.com will ship millions of roses – a number that will be topped only by Mother’s Day in May.
With such volumes, finding the perfect rose is no simple task. Cochran and team must manage a supply chain that begins with flower farms a continent away and ends with the delivery of a beautiful bouquet and a smile. The key to ensuring everything goes right — with the specs, the freshness, and the varieties — is having the right relationships.
“Our company’s mission is to help people develop more meaningful relationships, and do the same with our farmers,” Cochran says. “It’s all about building relationships over the long term.”
A reputation for quality roses
The perfect rose doesn’t happen by accident. It’s the result of countless choices, observations, and tests. The first step: Determining which of the estimated 30,000 cultivated varieties will perform best for demanding customers.
To that end, 1-800-Flowers.com has developed a long list of demanding specifications that it shares with the farms. The proprietary checklist — built from nearly 50 years of experience in the industry — includes everything from the dimensions of the stem and petal count to the color and appearance of the bud.
That list is shared with the handful of farms the company relies on for its flowers — and it’s enforced by a team led by Katya Chaparro, director of quality assurance at 1-800-Flowers.com. Together, Chaparro and Cochran have over 30 years in the industry.
“You walk nto a building, and people know you by what you've done over the past 30 years,” Cochran says. “And the big thing about Katya — and I would hope me, too — is that quality presence. They know that we're going to be talking quality before we talk cost.”
A rose’s journey on the farm
Finding the perfect rose begins on the farm. For 1-800-Flowers.com’s roses, that means a handful of large farms located high in the Andes on a plateau outside Bogota, Colombia. It’s the perfect environment for growing roses despite occasional weather and political challenges.
With the farms aware of Cochran’s and Chaparro’s specifications and everyone in agreement on the varieties, the roses are planted. And then everyone waits for the plants to mature.
Unlike with other flowers, humans can control the plants’ productivity. In advance of a seasonal peak like Valentine’s Day or Mother’s Day, they can boost the number of flowers by snipping them off when they emerge. This process, called pinching, causes the plant to generate even more buds.
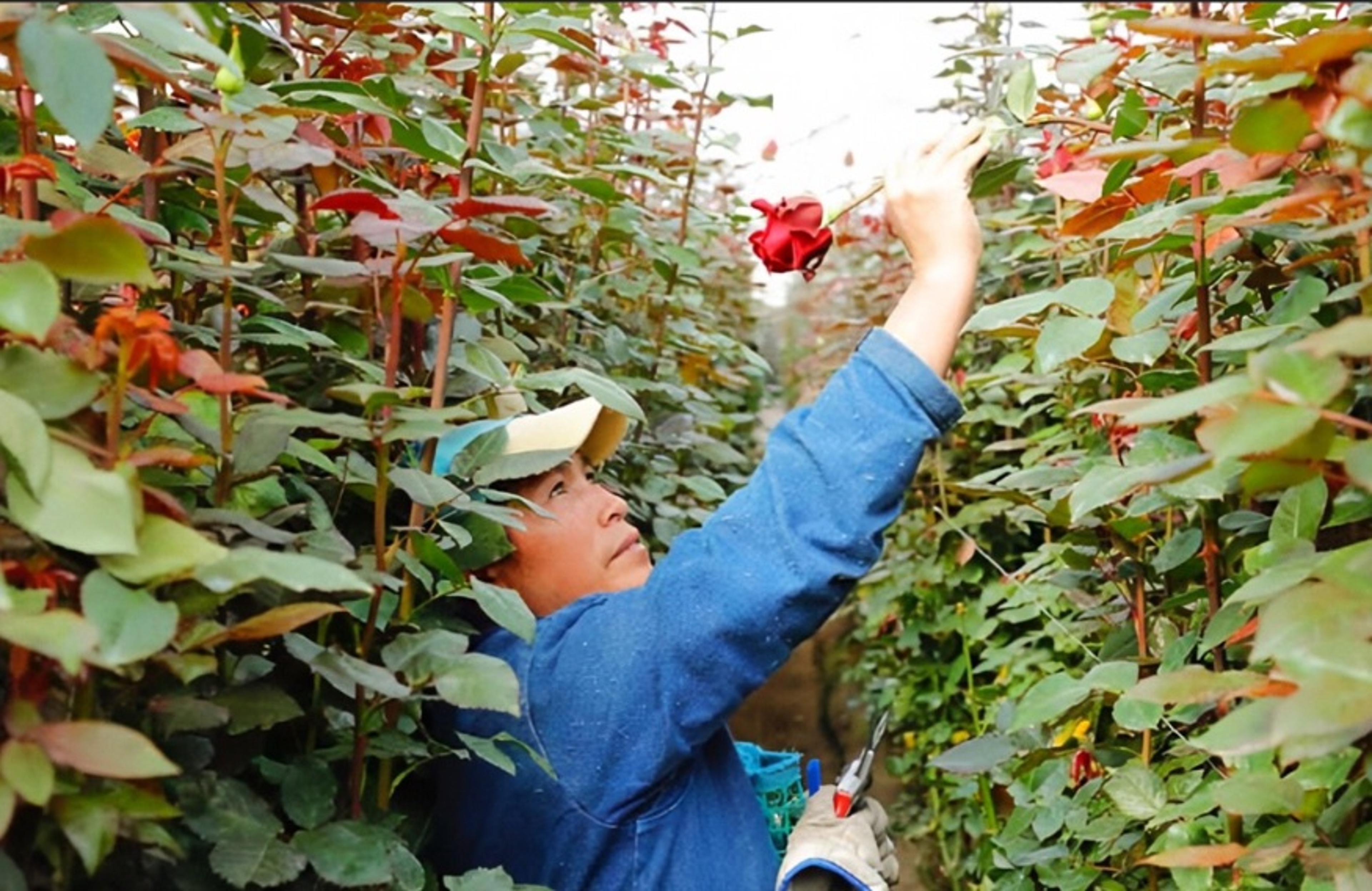
When production finally begins, crews begin by assessing each stem and picking the ones that meet the stringent specifications. They typically begin work at 6 a.m., just as the sun is rising.
“At first light, they start cutting, and they're really experts,” Cochran says. “The crew is looking to make sure the leaves are healthy. They're going to make that cut, put it in a basket, take it to post-harvest immediately, bring it down to temperature, and get it hydrated.”
From snip to ship
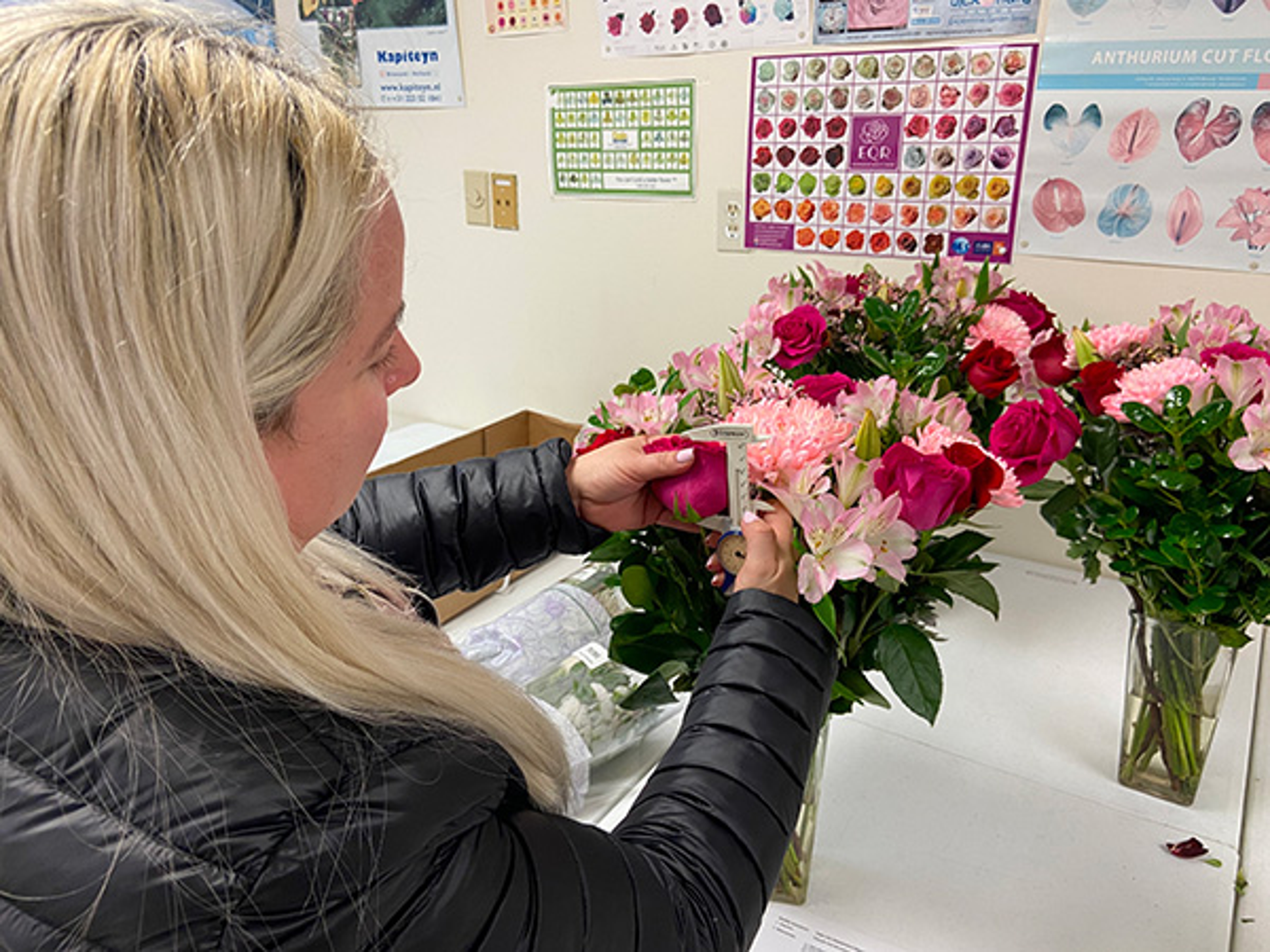
The farmers’ assessment of each stem is only the first inspection. In the post-harvest stage, the roses are cooled, examined, graded, and sorted by the growers’ inspectors and experts from 1-800-Flowers.com.“When we see something in Colombia that is not according to specifications, we reject it and the farm has to replace the flowers that are not compliant with the procedures,” says Chaparro, who works in Miami but often travels to Colombia, where she grew up.
What happens to flowers that don’t meet spec? “They sell it for pennies at markets in downtown Bogota,” Cochran says.
For those that remain, two things are critical: hydration and temperature. The stems are quickly placed in a solution that ensures freshness, stops bacteria and halts any six-legged visitors in their tracks. And they’re also cooled to an appropriate temperature to ensure that freshness lasts for as long as possible.
“When you warm up packed flowers, all those little metabolic clocks start ticking,” Cochran says. “It's kind of like an engine revving that you must slow down. You have to do it very carefully, and you have to do it quickly.”
Maintaining the cold chain
A consistently low temperature is critical as the flowers make their way from Colombia to Miami. Cochran and Chaparro refer to the supply chain as the “cold chain,” which means keeping the blooms at around 35 degrees.
Before the flowers leave the farm, they’re carefully wrapped and then packed in boxes that are loaded onto pallets and then stacked. The day’s shipments typically arrive at the Bogota airport around 7 p.m. — by which time the heat of the day has passed.
Overnight, they fly on cargo jets to Miami, another location not known for cool temperatures. Fortunately, the timing works out so they arrive before the sun rises. Within minutes, U.S. Customs inspectors check the shipments for bacteria, insects, and other issues.
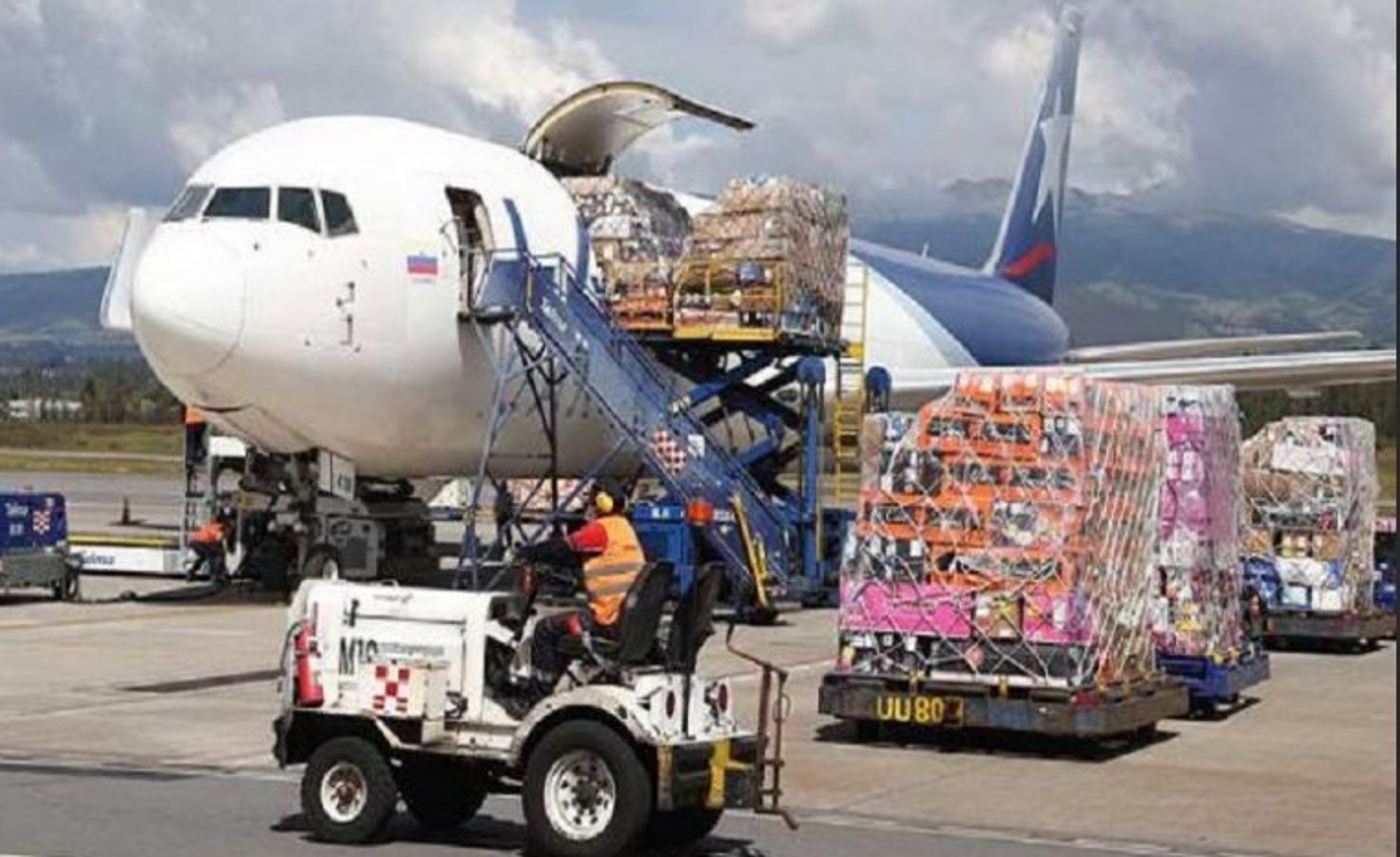
And then there’s Chaparro, who is peeling away boxes from pallets and inspecting the contents for any deviation from the agreed-upon specifications.
“A long time ago, I rejected 800 boxes from one farm during Valentine’s Day,” she recalls. “That is not the case anymore. The farms know they have to pay for it, and it’s a lot of money.”
The roses are typically stored for a day in a cooled facility, where they’re consolidated. Before long, they’re shipped in refrigerated trucks to fulfillment centers across the country.
“Literally, we're talking a day or two from when they’re cut from the rose plant at the farm,” Cochran says. “We’re talking about a really short window to get the flowers from Point A to Point B.”
Continuing the rose’s journey
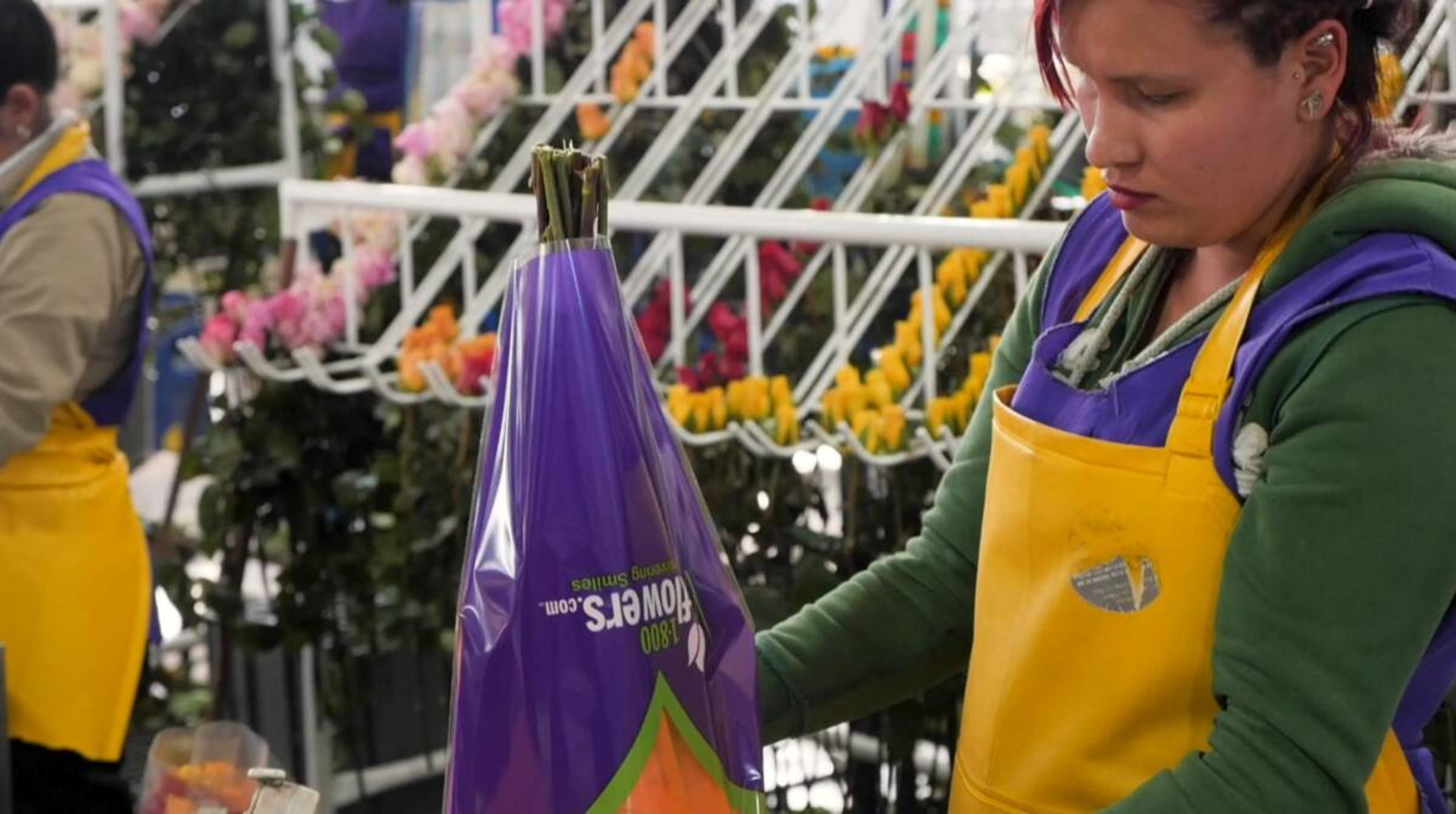
At the fulfillment centers, flowers are checked yet again before they’re shipped. And then attention turns to customers and the feedback they provide.
Some customers report their flowers are wrapped in plastic. Cochran explains that it’s a sign of freshness. “Those roses came directly from the farms to the airport,” he says. “They haven’t been handled by middlemen. They’re just straight from the farm.”
Other times, customers note what’s called “mechanical damage,” such as broken stems. This is caused by incorrect handling at some point in the supply chain, whether it’s the final delivery or packaging at the farm. In any case, problems are quickly identified and rectified.
This commitment to quality makes 1-800-Flowers.com stand out and ensures that it delivers millions of smiles on Valentine’s Day as well as the other 364 days of the year.
“I would say the big difference is in the detail of our standard operating procedures and the specifications that we provide to the farms,” Chaparro says. “We follow up every single day in Miami, in Bogota, or in every other place of inspection. And consistent quality is the result. That’s the key, and that’s the difference.”